Japanese culture is minimalistic and elegant. What can we learn from it, and how can we implement the best sides of this culture? How can we waste less and gain more from our learning activities? I will try to apply Toyota’s philosophy to accelerated learning.
Muda (Japanese term)
Muda is the Japanese word for waste or uselessness. It was accepted in Toyota as a critical optimization parameter and cultural value. This way of thinking was popular in industrial engineering in 1990s. Lean process thinking is defined as “Precisely specify value by specific product, identify the value stream for each product, make value flow without interruptions, let customer pull value from the producer, and pursue perfection. ”
To eliminate Muda the rooms in Japanese companies look very different from the rooms in Israeli companies. Everything is clean. The tables and whiteboards are shiny. There are just enough utensils to do the job and not more. There are a couple of small decore items, but that’s about it. The clothes, even casual, look like uniforms: very clean, properly ironed, and perfectly fit. In the conference room, people think before they talk. If there is silence, it is a thoughtful science of concentration and not an awkward silence.
Basically, a company with zero Muda is just the opposite of an Israeli startup. In an Israeli startup, most team members in basically clean but slightly stained and worn out t-shirts try to shout their ideas before each other, often not bothering to go to a conference room with mildly dusty tables. On the table, you will see coffee-stained pages, nonfunctional pens, leftovers of the morning meal, and presents from a 4-years old child to a parent. So, if we know that the Japanese are coming we spend a day cleaning up and shutting up.
Seven forms of waste
Taiichi Ohno, “father” of the Toyota Production System, originally identified seven forms of muda or waste:
- Inventory. The capital expense that cannot produce an income.
- Transportation. The risks are damage, delay, no added value.
- Motion. Usually the strain on manufacturing machines, but also on people.
- Waiting. When beginning of one task pending completion of another.
- Overproduction. Often due to safety margins, to have redundancy or to use large batch procession.
- Overprocessing. More complex or refined product than required.
- Defects. Discard products that do not pass quality inspection.
That is a pretty cool system to optimize the production of a large manufacturer. How does that apply to us?
The cost of storage
It is pretty clear that keeping too many products in a warehouse can be expensive as massive storage costs money. Americans have huge homes on expensive land with expensive heating and a huge environmental signature. Japanese usually have very small and modest homes, and pay a premium for location.
But is there a premium for other kinds of storage? For example, does it make sense to clean up the HDD or SSD? I am honestly not sure. In 1990s fragmentation was a huge deal. In 2000s SSDs were expensive. Nowadays, you can store pretty much everything except for video, and buy bigger disks when needed. It might be cheaper than your time. And the search is keyword-based, so you do not need to browse and keep things neat.
It is important to store files in one service, like Google Docs. If you have 10 different storage and backup solutions, that will cost you. Your stuff will be hosted from iOS and Android, dropbox, and iDrive, eventually generating a lot of expensive maintenance. At the same time, if you will try to synchronize 1 mil small files, the database of your backup solution will work extra time and might consume your computational resources or die.
Focus and transportation
A large part of Muda minimization deals with transportation. While this is important in the industrial setup, how important is it for a technological or service-oriented environment? We can deliver our product via a push of a button. Instead, I would emphasize the focus or attention span.
The force that drives the traffic in technology and service is the focus of the target audience. It is the transport layer upon which information arrives to us and travels back to our customers.
The question about the office space and its organization: does it maximize focus or steals the focus from the screen? In Israel, people prefer not to notice small unpleasant details, so an old yogurt package will drive the attention to screens. In Japan, the drive to clean up will be hypnotizingly strong. The same idea applies to the computer … I can easily keep 7 open windows of Google chrome with 100 open documents in each window. Most of the people I know will feel lost in these windows.
Focus is not a physical transport and the costs are very subjective… If someone eats within 2 meters from me, I cannot work. At all. Usually, I take a break, no matter how important and urgent my task is.
Motion and emotion
We are less resilient than we would like to think. There are stress and burnout, and even mild emotional issues might overpower us. What if we resent what we need to do, or do not understand why we are doing it? How about toxic people we have to work with? And do not forget the large bag of anxieties all of us carry…
We invest a lot of unnecessary effort to deal with our emotional limitations. Obviously, emotions are not necessarily wasteful. Without passion any kind of entrepreneurship is unimaginable. Love and respect make teamwork easier and more satisfying. We are humans, working with humans for humans. So the wisdom here is not eliminating emotions, but managing them effectively.
Waiting
We need to wait occasionally. For example, a programmer needs to wait till the software compiles and the execution reaches the breakpoint. Most of our waiting encounters are short, maybe 5 min long. If we plan to wait, we can call it a Pomodoro break and do tasks. What about unplanned waiting?
Usually, we cannot quite switch the context in the middle of debugging software or waiting for a client to read our proposition. This time is lost and we should better accept it. We can however rest. Notice the breathing and ergonomy, go over the strategic goals and such…
A good design of a process will probably eliminate waiting. A great design will control the waiting periods and create Pomodoro breaks. Realistically we should at least accept some waiting periods and not be bothered by them, while slowly reducing these periods.
Overproduction
I am always surprised by people reading thousands of books. Why do you need that? I understand reading a couple of books when learning a new subject or for fun. I also understand scanning through a large number of articles, hoping to stumble upon something useful. But why read thousands of books? This is not very effective, as eventually, our mental structures start to merge and collapse.
Consider a royal family. As long as it has a summer palace and a winter palace, it may take care of the real estate. Now suppose there is a resident villa in each city of the kingdom. What exactly is going to happen in each of those villas? Some locals will probably abuse the places and the funds. Some places will never be visited.
Now, what about us? How many mental palaces can we realistically revisit and maintain? Maybe two mental cities at the same time… Maybe more, but definitely not thousands.
Some overproduction deals with redundancy, some with creativity, and some with abundance. It cam
Overprocessing
How many words and details do we need to remember something? As more information is added, the memorization gets very complex. Do we need 100% retention? Maybe we need to read the article, choose 20% of it, and get 100% retention over 20% of the content. And possibly we do not even need to remember the article the next day after reading it.
We tend to do a lot of unnecessary steps. Possibly we think of them as embellishments, or maybe we do not notice them. Often we are not aware of the alternatives.
For example, we need to revisit everything we want to remember several times. We can simply read it, we can use cue cards, or we can write about it. If we write about it, we have something of value as a byprocess. So why not use this approach?
Defects
Acquiring some skills, only to relearn them later due to bad habits is painful. There are many useful iterative approaches. Relearning is not one of them.
It is much better to spend a bit more time understanding the subject, hire a coach (like 1:1 with Anna) or read advanced materials. A small financial investment can save a lot of headaches.
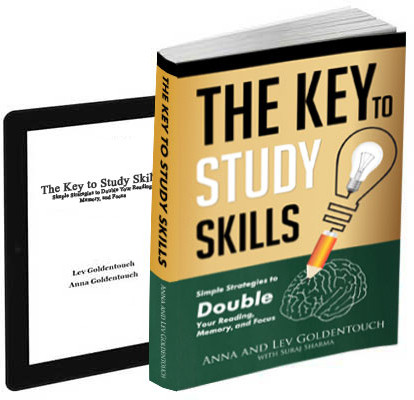
Get 4 Free Sample Chapters of the Key To Study Book
Get access to advanced training, and a selection of free apps to train your reading speed and visual memory